2 Strategic Ways to Avoid Hydraulic Emergencies
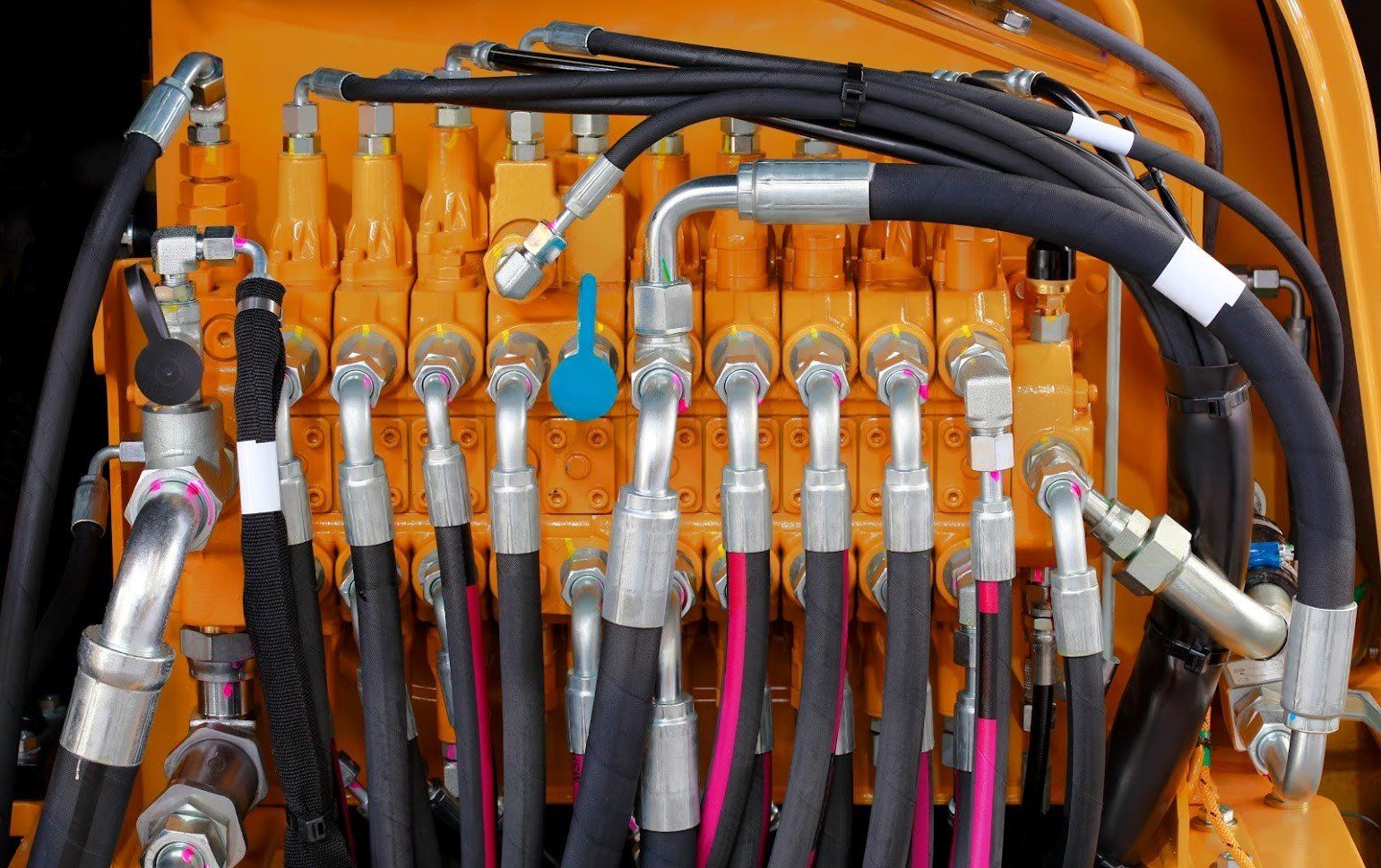
Hydraulic systems are dynamic machines with many moving parts. Often, one bad component can affect an entire system and lead to inefficiency or unnecessary downtime. An emergency that shuts down workflow can be costly when production ceases or even dangerous if nearby operators receive injuries.
Fortunately, hydraulic emergencies can be preventable. The right knowledge enables operators and other workers to spot a problem before it worsens. Learn more about these two strategic ways to avoid hydraulic emergencies.
1. Avoid Contaminants
Contaminants like dirt and water within a hydraulic system can ruin closely fit moving parts and cause clogs or leaks that jeopardize efficiency. Consider the following simple habits that keep invasive contaminants from entering and harming a system.
Inspect Oil Daily
Sometimes, oil will adopt a milky or foamy appearance from the introduction of air. Unfortunately, air inside a system means the presence of moisture, which becomes obvious after a system cools. Condensed air mixes with oil, and the resulting milky appearance means water contamination is present.
Use Correct Filters
Around 70% of hydraulic failures are from contaminants. If a filter is not the proper size and fit, your system could become part of this statistic. Remember, filters are rated for both particle size and dirt-holding capacity. Your filter may allow smaller particles to escape even though it can hold a higher weight of larger particles.
Be mindful of your actual system run time when you consider the manufacturer's recommended filter maintenance. You may need to change filters on valves, actuators, and pumps more often if you run your hydraulic system 24/7 rather than eight hours per day.
Keep Clean
Operator and maintenance staff may unintentionally introduce contaminants into new, clean oil. You can avoid this by adopting the mantra to keep clean. For example, the need to change or check oil levels often allows dirt to enter. Clean the area first around hydraulic filters, fill plugs, and dipsticks before their removal to keep contaminants out.
Only pour from the original container into the system. Then, tightly seal stored oil containers to prevent the entry of contaminants.
2. Avoid Hose Failure
Much like human veins and arteries, hydraulic hoses perform similar tasks as they deliver fluids throughout key hydraulic machine components. Failing hoses cannot distribute necessary fluid, which can lead to limited efficiency and loss of production. Even worse, a sudden or unexpected hose failure releases highly pressured fluids that may be toxic or hot.
Several conditions may lead to hose failure.
Insufficient Insertion Depth
Poorly joined hose assemblies can cause a fitting to suddenly blow off. This dangerous scenario may lead to a swiftly whipping hydraulic hose with the potential to waste fluid, make a slippery mess, and spray nearby workers. Instead, fully push in fittings to meet the recommended insertion depth.
Dirty Assembly
Contamination that enters a hydraulic hose assembly tends to abrade and weaken inside hose diameters, which later leak. This happens when tiny particles enter the hose as it is cut and then not properly flushed. Make sure inner hoses are very clean before fitting insertion, and securely cap ends to prevent further contamination.
Exterior Abrasion
Disproportionate friction during operation when hoses come into contact with other objects can make a hose appear noticeably worn. Sometimes, the protective outer cover is torn or reinforcement wiring is visible. Replace a badly deteriorated hose. Fortunately, strategically placed protective covers can protect new hoses from future damage from other objects.
Sometimes, the best maintenance plans fail to prevent a hydraulic
emergency. Contact the experts at Miller Hydraulic Service, Inc., if you suspect your hydraulic system may be in need of an update.