4 Types of Hydraulic System Tests to Keep Machines Running Smoothly
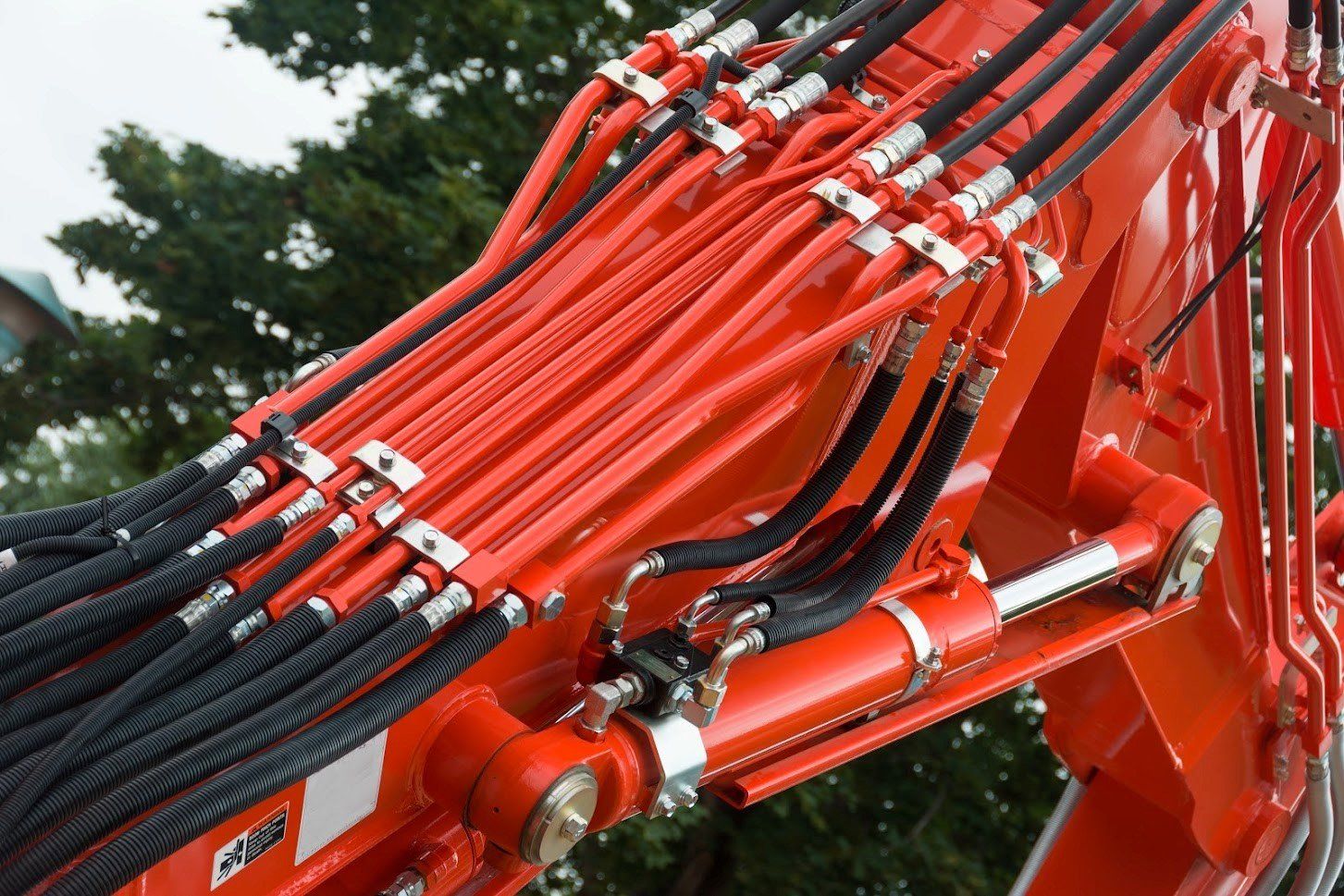
The pressure and materials in hydraulic machines creates the need for maintenance and service to ensure they run properly. Testing is an essential part of your company's hydraulic use. Proper testing will ensure the systems run for years, and you avoid major disasters that could lead to operation downtimes or full replacement.
Hydraulic testing breaks down into several categories. Learn about each form of testing and understand what testing is necessary for your company to thrive.
1. Water Tests
Hydraulic systems may include a wide variety of liquids with the machines. When you perform initial tests on equipment, one of the more basic elements is water. When equipment leaks or spills, simple water is much easier to clean up than oils or chemicals. A water test is essential for testing the pressure and leaks within a hydraulic system.
Water leaks are easy to spot with special testing equipment. Testing companies can track the location of the water leak and follow pressure measurements that may indicate when a problem has occurred. When water is used, technicians can easily add more, increase pressure, and see the performance.
They can make adjustments and fully drain the water without the need to worry about proper disposal or exposure to excess chemicals.
2. Repair Tests
When repairs are necessary on a hydraulic system, you shouldn’t just replace the part that the system needs and continue operations. Any major change requires testing. A testing company can inspect the repairs and ensure the parts are installed properly before the testing even begins. You do not want more damage to occur if a part is not installed correctly.
Testing tools can also check to ensure the longevity of the repair. You do not want a new part or function to simply act like a bandage on the whole system. Different tests will focus on the longevity of a repair and ensure the repair can last for the long haul. If the tests do not warrant optimal results, then you may consider other options like full machine replacements.
3. Start-Up Tests
If you have purchased all new equipment or started a whole new company, then start-up tests are ideal. Before operations are up and running, full testing is essential. The reports will detail the performance of machines and ensure everything operates smoothly. The testing process requires a minimal crew.
The last thing you likely want to worry about is hiring employees, starting operations, and then shutting down again due to errors. You will end up wasting a lot of time and resources. The start-up tests you run will often be in the early days of the machines. If any major problems occur, you will likely have coverage through parts and labor warranties if they apply to your equipment.
4. Test Standards and Optimization
Every now and then, consider tests for machines even if they operate smoothly. The hydraulic machines you have may run, but their performance may not be up to the typical standards. Testers have data and a set of standards for which the machines should reach. Many are from the National Fluid Power Association (NFPA) Standards for equipment.
From the standards, test technicians can offer recommendations for improvement. With some improvements, your system can operate more efficiently and use fewer energy resources. Recommendations may include simple repairs or system tweaks that require no repairs at all. The tests can make a big difference in your overall operations.
For more information on hydraulic testing, contact us at
Miller Hydraulics Service, Inc. We can help set up testing and provide you with professional services, no matter what type of testing you seek for your business.