4 Ways Hydraulic Fluid Can Get Contaminated
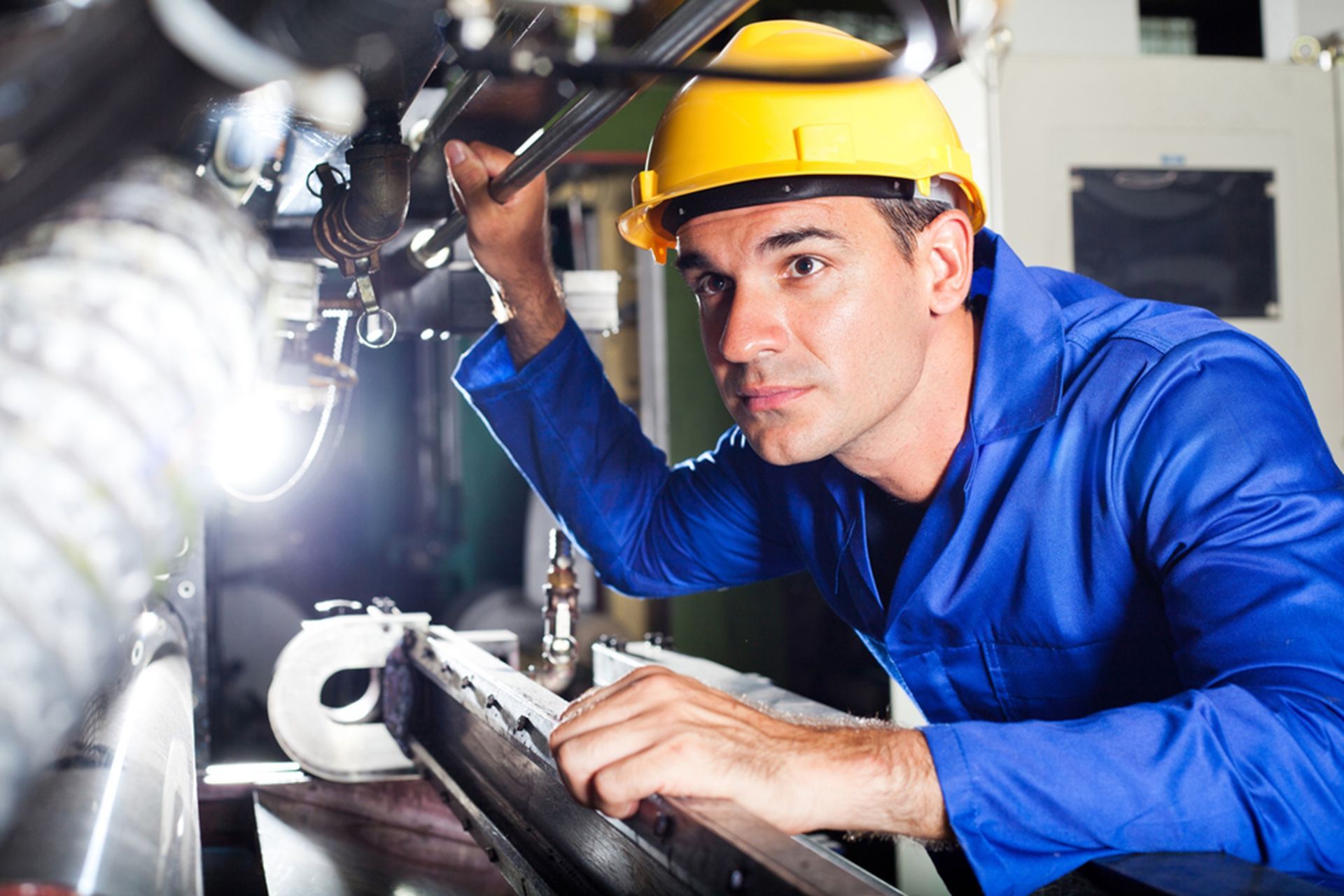
Hydraulic systems are widely used in various industries for efficient power transmission capabilities. Hydraulic systems rely on clean and uncontaminated hydraulic fluid to ensure optimal performance and longevity. However, even with the best maintenance practices, hydraulic fluid contamination can occur, leading to compromised system performance and potential damage.
By understanding these contamination sources, you can take proactive measures to prevent or address them, safeguarding the integrity and reliability of your hydraulic system. Here are the four primary ways hydraulic fluid can become contaminated.
1. Contamination During Production
Several processes and conditions can lead to contaminated hydraulic fluid being used in manufacturing. The purity of the fluid supplied by providers is the primary consideration. According to the ISO 4406 Cleanliness Code, the typical hydraulic fluid carries a cleanliness rating between 17/16/14 and 20/18/16, which is still better than most equipment manufacturers suggest. But these hydraulic fluids still lack sufficient purity for use in today's hydraulic systems.
Hydraulic fluid may get tainted at any point during the manufacturing process, including during processing and mixing. The introduction of pollutants into the fluid can result from incorrectly designed equipment, machinery, and tools.
Furthermore, dirt, dust, and debris can enter the hydraulic fluid without proper safety measures. Hydraulic fluid is also vulnerable to contamination from various sources, including leaks from other industrial processes.
Contamination that begins with the supplier from the fluid's production conditions are beyond the buyer's control. Thus, filter all fluids before they enter the hydraulic systems to prevent system inadequacies.
2. Contamination Built In
Welding slag, milling swarf, bits of Teflon tape, and too much sealant can all contribute to built-in hydraulic fluid contamination during assembly or maintenance. This contamination is notoriously difficult to detect and often leads to undesirable system behavior like fluid leakage or pressure decreases. Cleaning the hydraulic fluid beforehand is crucial for avoiding immediate and long-term damage to machinery.
Regular inspection and replacement of the filters can help prevent the accumulation of impurities in the hydraulic system, which can hasten the system's decline. Also, install system components with extreme caution to avoid introducing any of the above pollutants, such as bits of Teflon tape or too much sealant, into the system.
3. Contamination During Storage
When the hydraulic fluid gets subjected to weather changes, debris, dust, and humidity during storage, either because of breathing or improper sealing, the fluid becomes contaminated.
Incorrect sealing allows contaminants to enter the fluid because the container was not shut tightly or was left open. Breathing occurs when moisture enters the interior of a sealed, watertight plastic container due to temperature changes.
Always store hydraulic fluid in a sealed container at a constant temperature to prevent contamination from the storage environment. If you need to keep the container outside, lay it on its side to stop water from pooling on top of it. Temperature control is not the only solution since you should regularly check the integrity of the containers' seals.
When moving hydraulic fluid from one container to another, take special precautions to prevent fluid contamination. Thoroughly clean the storage containers before you pour the fluid into them.
4. Contamination During Fluid Transfer
The surrounding environment and the method of transmission might lead to hydraulic fluid contamination during transfer. Fluids can pick up dirt and moisture from the atmosphere if transported in an unsanitary setting. Failure to flush the system before introducing used or new fluid might also exacerbate contamination. Chemical interactions between different fluids can also taint the entire mixture.
Ensure there is no dust or debris in the area, and flush the whole system before you add hydraulic fluid to minimize the risk of contamination. Also, do not leave the fluid's cover off longer than necessary.
Contact us at
Miller Hydraulics Service, Inc for hydraulic parts and services if you find your system contaminated. We serve businesses located in all of Central and Northern Illinois and North Western Indiana.